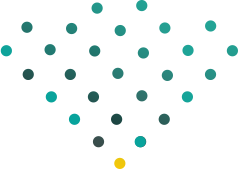
Real Time Condition Monitoring of Electric Propulsion and Generation System Using Passive Battery-Free RF Temperature Sensor
Reamonn Soto, Joshua McConkey, Swadipta Roy, Sreekala Suseela, Taofeek Orekan, Sensatek Propulsion Technology, Inc. Daytona Beach, USA {rsoto, josh, sroy, spapali, torekan, }@sensatek.local
Abstract— Real time passive RF temperature sensors used to wirelessly monitor the temperature of components such as rotors, stators, and windings used inside of generators and motors within electric propulsion systems are presented here. Sensors have been installed onto windings which rotate at full speeds (6,000 rpm, 5,000g) and temperatures above 140°C. Full system tests on electric motor rotors in multiple motor rig spin tests have been performed at speeds to 10,000rpm and 16,000g along with temperatures above 175°C in the presence of very strong (> 1 Tesla) and dynamic magnetic fields. Rotor temperature was monitored and experimentally evaluated and demonstrated. The system uses passive wireless sensors that can attach to the windings, rotor, magnets, disk, or shaft of a generator or electric motor used in onboard electric propulsion systems. Using a magnetically insensitive wireless measurement system, the temperature was monitored and recorded in real time. The sensors were interrogated using high temperature silicon dioxide co-axial cable antenna using radio frequency resonance-based sensing. The sensor-antenna set up was employed for temperature monitoring in a high magnetic flux metallic environment. Real time temperature monitoring was provided by indigenous software (Turbotrack).
Keywords — Passive wireless sensors, Real time temperature monitoring, Electric propulsion systems
I. INTRODUCTION
Electric propulsion motors are changing different industries such as aviation and shipping by reducing fuel costs, eliminating direct carbon emissions, enabling affordable tests, and providing a sustainable alternative to traditional engines. Importantly for the shipping industry, electric motors can provide competitive power and more efficient cruising speeds and can be used for hybrid ship propulsion systems that combine conventional and electric generators and motors. Additionally, electric propulsion systems are more reliable, easier to maintain, and more cost-effective than traditional propulsion systems. These three aspects are likely to increase air safety. In the shipping arena, more electrified propulsion systems offer the benefits of higher efficiency (lower fuel costs), broader fuel flexibility, and significantly lower maintenance costs.
As solutions involving battery weight and in-transit electrical generation become better and more widespread, the utility of these electric propulsion motors is increasing. Many companies are now vying to create commercially viable electric engines, with emphasis on efficiency, low maintenance, and reliability. One of the most important aspects of optimization for these electric motors involves understanding and controlling the heat generated during their operation. Excessive heat can harm an electric motor or electric engine in a number of ways, including thermal overload, reduced efficiency, reduced lifespan, insulation damage, increased stress on the cooling systems, reduced performance and reduced reliability. Real time monitoring of electric propulsion units is of utmost importance, as hassle-free longevity of the system ensures smooth operation with reduced maintenance cost. The shipping industry invests billions of dollars each year on system maintenance.
While there is a pressing need for monitoring the temperature of the rotating internal components of electric propulsion and generation systems, there are no such non-intrusive, passive, and robust technology until now that can effectively and accurately achieve this feat. Traditional methods using thermocouples are not very effective for rotating applications because one must use rotating active electronics or slip rings to utilize them on rotating components. Active electronics add significant mass, are difficult to operate in high magnetic fields, and have a limited lifetime due to reliance on batteries. Slip rings are very expensive to install and lack durability for long term monitoring. Many thermocouples also struggle with the strong electro-magnetic interference and induced currents inherent within electric motors and generators.
Passive wireless sensing technology is a promising solution to this problem can operate without an external power source. With this technology, it is easily possible to monitor the vital of the system even in difficult to reach locations [3]-[6].
Sensatek wireless sensors can also help provide key information in rotating, high-magnetic-flux environments to allow the highest levels of efficiency optimization. The Sensatek wireless sensors and antenna are both completely insensitive to high-powered, fast-changing magnetic fields. The Sensatek Wireless Temperatures System with the Turbotrack software can make major contributions to the optimization of electric motor designs. By applying Sensatek’s passive wireless sensors directly onto rotating magnetic, metallic, and insulating parts, real time continuous temperature monitoring can be done without slip rings and without any electromagnetic interference with the E measurements.
Specifically, data from Sensatek’s system can be used to:
1. Optimize magnet dimensions (Permeance Coefficient): By knowing the maximum temperature the magnets can actually reach, one can optimize the shape and thus the mass and profile of the magnets in many types of rotors [7]. Sensatek wireless sensing technology can be able to make direct measurements to provide empirical data at any speed and power settings of a motor.
2. Optimize cooling flows: Empirical data generated employing Turbotrack software can be used to understand the exact heat transfer rates to the most important rotating parts. By optimizing this across the entire operation range of the motor with real-time data, cooling air can be adjusted, and efficiency gains can be realized [8].
3. Optimize magnet and rotor lamination and segmentation optimization: Using Sensatek sensors along with existing simulation suites, we can develop thermal boundary conditions to have much more direct knowledge of the magnitude of eddy currents in magnets and rotor metal. By detecting the heat generated by eddy currents, the Sensatek sensors can provide information whether lamination and segmentation is even necessary or can be reduced. If those can be reduced, then the magnetic strength of the magnets can be increased. In case of laminated rotors, a reduction in lamination or lamination separations can help increase the reluctance of the rotor [9]. Either of these can significantly increase electric propulsion motor efficiencies.
More accurate knowledge of actual temperatures on key stationary and rotating structures in the motor can provide significantly more design margin for efficiency gains. For example, if an engineer knows with certainty that the permanent magnets never go above 115 °C in any operational condition, then they can be more aggressive in reducing weight, lowering gaps, foregoing magnet segmentation, or increasing coil current and power. Then the efficiency of the motor can be increased [10]- [11].
Sensatek designed and demonstrated a passive RF temperature sensor to measure metal, magnet, and insulator temperatures to within 0.4 °C accuracy via wireless interrogation via a small, 3.6mm antenna that can read the sensor during its closest path from a distance of 10-30 mm. The sensor and the antenna set up were designed so that the system remains unaffected by the strongest magnetic fields. The sensors are typically 11 mm X 15 mm and are 0.5 mm thick, and other custom sizes (down to much smaller sizes) are available upon request and can be mounted on any magnetic or non-magnetic surface. A 10 mm X 7 mm dimension sensor has been shown in Figure 1.

Because they are wireless, the sensors can be mounted and read on rotating portions of the electric motor; no matter how fast the motor is spinning. These light (0.4 g) sensors require no battery and will last for many thousands of hours. They are energized and interrogated by Sensatek 304L/SiO2 antennas, with diameters as thin as 2.3 mm, allowing them to be inserted into the most intricate locations. These sensors can withstand g-loads above 50,000g, meaning engine RPMs above 20,000 are feasible measurement targets, at almost any radius. The sensors are read on a timescale of 50 microseconds, so they can be read with an accuracy as good as ±0.4 °C (specified better than ±0.9 °C) over a very wide range of speeds. No rotating antenna is needed to be added to the sensors. Multiple sensors and antennas can be used simultaneously, and they don’t interfere with each other. Thus, Sensatek provides a non-intrusive, geometry specific, durable, and very accurate way to assess temperatures in both stationary and rotating sections of an electric propulsion motors. A real time application of Sensatek’s wireless temperature sensing technology is shown in Figure 2.

These passive sensors weigh less than 0.5 g and can be affixed to any rotating or stationary surface. Using Sensatek’s -150 °C to 900 °C silicon dioxide 2.3 mm or 3.6 mm diameter antenna, the sensors can be excited and interrogated in real time even in very tight spaces. The sensors can be read at any rotational speed in real time with accuracies of ±0.4% of max reading, or ±0.9 °C. The sensors can be epoxied in place or affixed in a myriad of other ways, and the antenna can be glued, strapped, or simply positioned in place. Sensatek has multiple antenna models that have a bendable stiffness that makes test setup quick and easy. The 5’, 10’, or 15’ long antenna allows flexibility of the set up so that the associated hardware can be placed far from the test article, even outside any vacuum spin pit.
The Sensatek system is completely impervious to electromagnetic interference (EMI), even to very strong electromagnetic fields that are rapidly changing. Neither the sensor nor than antenna contains a completed conductor loop, and their RF operation means drifting grounds simply don’t matter. Accurate temperature measurements are obtained regardless of the environment, up to 600°C. Sensatek’s sensors can also be read wirelessly through most non-conductive materials.
We demonstrated here a novel technology in order to continuously monitor critical components such as windings used in electric propulsion system using passive wireless sensors in real time frame. The technology utilizes RF sensors that are mechanically bonded to the rotating parts and wirelessly interrogated by a high temperature silicon oxide co-axial cable terminated in a high temperature antenna. The response is recorded in real-time featuring a time versus temperature plot which allows continuous monitoring of the blade temperature. The technology can continuously collect and save temperature and other parametric data employing a Sensatek developed software (Turbotrack) which enables the system engineers not only to perform predictive maintenance of the system, but also ensures the reliability and safety of the same as well. By gaining accurate, EMI-resistant, wireless measurements on rotating and stationary parts, one can reduce the temperature uncertainties to almost zero and design more aggressively efficient electric propulsion motors for different purposes.
The development of real-time passive wireless temperature sensors for electric propulsion systems is a significant advancement in the field of electric motor design and optimization. These sensors can monitor the temperature of rotating components, such as rotors, stators, and windings, in high magnetic fields and at high speeds and temperatures, without the need for active electronics or slip rings. This technology can provide crucial information to optimize the design and operation of electric motors, resulting in increased efficiency, reduced maintenance costs, and improved reliability.
The shipping industry is increasingly adopting electric propulsion systems to reduce fuel costs, carbon emissions, and maintenance costs, and to improve safety and reliability. The development of these sensors provides a promising solution for monitoring the vital parameters of electric propulsion systems and optimizing their performance. The Passive battery-free RF temperature sensor, combined with Turbotrack software, offers the potential to optimize magnet dimensions, cooling flows, and magnet and rotor lamination and segmentation, which can significantly increase electric motor efficiencies. Overall, this technology has the potential to revolutionize the field of electric motor design and optimization, and enable the widespread adoption of electric propulsion systems in various industries.
The use of passive wireless temperature sensors to monitor the temperature of components in electric propulsion systems such as rotors, stators, and windings. The sensors were able to operate at high speeds, strong magnetic fields, and temperatures above 140°C has been demonstrated. The system uses a magnetically insensitive wireless measurement system, and real-time temperature monitoring was provided by indigenous software (Turbotrack). Passive wireless sensing technology is a promising solution for monitoring the temperature of rotating internal components of electric propulsion and generation systems. The Sensatek Wireless Temperatures System with the Turbotrack software can make major contributions to the optimization of electric motor design and operation.
II. WIRELESS TEMPERATURE MONITORING SETUP
The materials and methods for wireless condition monitoring has been divided into three parts: the ceramic based sensor, the stationary interrogation antenna, and the data collection and recording using Turbotrack software. These are explained in the following sections:
A. Wireless Ceramic Passive Sensor
The wireless passive sensors used for temperature monitoring are fabricated based on co-fired ceramics. Though the temperature requirement for this purpose is not that high (i.e., not more than 220 o C) but Sensatek’s ceramic based sensors can withstand and function properly up to 600o C. These ceramic sensors have other advantages such as high temperature survivability, excellent oxidation resistance, and flexible manufacturing capabilities. Sensatek has several options of sensor materials for low temperature as well as high temperature condition monitoring. Whereas specific composite material like FR4 is good for low temperature applications, PDC and co-fired versions of Sensatek’s proprietary SelikenTM ceramic find applications for high temperature and high magnetic field environment monitoring.
SelikenTM ceramic plates of a particular thickness and based on simulated design small coupons are cut and metallized by applying either silver (Ag) or platinum (Pt) conductive pastes. After applying the Ag or Pt conductive pastes the coupons are dried and sintered inside a Thermo-Fisher Scientific box furnace. The furnace can be programmed prior to starting the firing cycle, so manual intervention is not required during drying and sintering. Detailed sensor design and firing schedule are not discussed here due to proprietary information infringement. Selection of the conductive paste for metallization depends on the ultimate operating temperature of the sensors. The sensor was designed by employing CST Microwave Studio software and repeated simulations were run to ensure its optimal performance which in turn is quite helpful in providing accurate and reliable temperature data.
These sensors are an integral part of the temperature monitoring set up developed by Sensatek. As described in [6], a slot antenna is inscribed on the RF passive wireless sensor, integrating a cavity resonator with a transceiving structure, both inherent to the sensor itself. The dielectric constant or relative permittivity (εr) of these ceramic based sensors changes with the temperature and Sensatek developed these RF wireless sensors by exploiting this characteristic along with inductive resonant geometrical structures within the sensor body. When the temperature of the sensor installed on the monitoring unit increases, the dielectric constant of the ceramic substrate increases, causing the corresponding resonant frequency of the sensor to decrease. By recording that change it is possible to monitor temperature in real time scenario. Figure 3 depicts change of dielectric constant with temperature for selected ceramic materials. It is clear from Figure 3 that the variation of dielectric constant with temperature is almost linear for the selected ceramic materials which is quite suitable for this application. Seven-point calibrations of the frequency-temperature relationship allow Sensatek to have very accurate calibration curves which also capture any small non-linearities.

Sensatek devised some selected methods for bonding the sensors to the monitoring unit. These methods are very quick, robust, and mainly vary depending on the application temperature. JB Weld 8272 and M-Bond 600 are typical adhesion methods for adhering the sensors with high strength and durability to magnetic, magnetic, and insulating parts that will be rotating at temperatures up to and including 250°C. Figure 4 shows a fabricated RF passive temperature sensor bonded on the rotating windings of a C-130 generator illustrating the on-field application of the sensor. This new and innovative approach eliminates the need for electrical power or wiring and reduces the cost and complexity of the existing high temperature sensing technology by employing these passive wireless sensors. The need for slip rings (to measure temperatures on rotating equipment) is drastically reduced or eliminated.

B. Modified Coaxial Cable Interrogation Antenna
For successful measurement of sensor frequency, a robust interrogation antenna is required for transmitting and receiving radio frequency (RF) signal from the sensor. The interrogation antenna transmits a wideband microwave signal to excite the sensor. The sensor re-radiates the frequency component at the sensor’s resonant frequency, which is received by the interrogation antenna. When the temperature of the monitoring unit with the attached sensor increases, the sensor’s resonant frequency changes, and this change in resonant frequency is captured by the antenna. The shift in resonant frequency is used to obtain the temperature of the material where the sensor is placed.
The interrogation antenna must be able to operate at high and dynamic magnetic fields to withstand the harsh operating conditions inside electric motors and generators. In addition, the antenna must have a high bandwidth in order to capture the significant frequency changes of the sensors over temperature. To meet these requirements, Sensatek designed a semi-rigid coaxial slot antenna using a semi-rigid, silicon dioxide (SiO2) coaxial cable obtained from Times Microwave Systems. To ensure that the antenna can operate reliably at high speeds and to avoid damages to the inner conductor of the coaxial cable, slots were introduced along the outer body of the cable (Figure 5). Parametric analysis was performed in CST by varying the number of slots, the length of each slot, and the gap between the slots, and the optimized design was chosen for fabrication.

The coaxial antenna was excited using R-140, a 1-port Vector Network Analyzer (VNA), from Copper Mountain Technologies. The antenna was connected to the VNA, and its return loss performance was evaluated using the RVNA software. Figure 6 shows the S11 of the coaxial slot antenna measured in free space. As can be seen from the figure, the antenna exhibits a wide bandwidth from 3.5-14 GHz, with an S11 value less than -10 dB. The sensor resonant frequency captured by the interrogating antenna was found to be 4.5416 GHz which is shown in Figure 7. By using proprietary Sensatek RF algorithms, we isolate the sensor response from the reflections of the surrounding metallic, ensuring accurate and reliable temperature measurements.


C. Data Collection and Recording Using Turbotrack Software
Sensatek designed and prototyped a data acquisition system (Turbotrack) built in National Instrument LabVIEW, a configuration-based software tool which acts as data flow handling and visualization environment for creating real-time testing applications more efficiently. LabView provides the functionality required to implement real-time application and automate the process of obtaining raw sensor data produced by the Copper Mountain Vector Network Analyzer (sensor interrogator). The raw resonant frequency data from the sensor to the interrogator was turned into a real-time stream of temperature data and processed through the LabVIEW GUI.
In order to sync the interrogator with the GUI, the programming documentation for the VNA was used to determine the data type. A data logger interface is also implemented in the GUI which provides the user with a fast way to collect data and save in different format for offline processing (Figure 8). The developed GUI is capable of displaying the real-time sensor frequency response and updating the graphs recording the temperature over time.
The following functions are implemented in the GUI interface; 1. Real-time, instant view of temperature data during test with digital reading, rolling updated plot and chart, and 2. Fully automated real-time display of time stamped data and wireless sensor temperatures. In addition, the software encompasses multiple modules to handle functions that include calibration, display, engineering unit processing, data logging, and data management to organize software into various functional areas for the purpose of providing the modularity. In addition, the GUI will track and generate the temperature data of sensors with time stamps associated with system and store them in a specified location or online.

The real time temperature profile from Turbotrack software has been shown in Figure 8, showing the performance of a 1100°C rated sensor and antenna in an oven test up to 1075°C.

Sensatek calibrated its sensor before field installation by using a laboratory-based box furnace set up (which is not shown here) and based on that calibration file Turbotrack can monitor temperature accurately and reliably. Figure 9 shows a sample calibration curve that was generated in the laboratory simulating the practical condition for a particular senor antenna set up. As mentioned previously, a linear relationship is obtained between the sensor resonant frequency and temperature which is quite similar in comparison to the theoretical data available. In general, the resonant frequency of the ceramic based sensor shifts towards the left as the temperature increases. During operation Turbotrack collects and records the transient resonant frequencies and also the temperatures of the sensor in two separate Excel files for offline data interpretation which can help industries to monitor their tools periodically for predictive maintenance.
Based on Sensatek precision calibration curves, Turbotrack software tracks temperature accurately in real time and thus continuous monitoring of the rotating parts is easily achievable. Also, this technology helps industries to identify any anomalies or potential failures by continuously collecting and analyzing temperature data in real time scenarios. This enables operators to take action before structural collapse and increases the safety and life expectancy of the rotating machines.
III. CASE STUDY
Recently, Sensatek performed a test inside a hybrid electric propulsion system in both stationary and rotating conditions. The purpose of this test was to compare the performance of Sensatek’s sensors versus high temperature thermocouples and pyrometers while the test item was in stationary condition and heated inside propulsion system and when the item was rotating.
The sensors were mounted in two locations: on the rim of a magnetized cylinder and inside the cylinder near its back. A small space was kept clear in order to route the antenna to the inner cylinder area, but this still required significant bending and midair suspension of the antenna in order to be within 1-2 cm of the sensor. The antenna installation near the rim also had an antenna mounted suspended above its position. Pictures of the installation cannot be published due to proprietary information.
The Sensatek sensors accurately reflected the metal temperatures and is comparable with the thermocouple readings mounted next to them in the stationary tests, and also accurately reflected the expected temperatures during the rotating tests. In stationary test, the Sensatek’s sensor was typically within 0.8 °C of the metal thermocouple, and for extended periods was within 0.2 °C.
During rotating tests at extended oven dwelling times, Sensatek’s sensor reflected the thermocouple temperature within 0.8-1.4°C. The Sensatek sensors had stable readings throughout the testing. Figures 10 and 11 illustrate Sensatek sensors response with time during stationary and rotational conditions, respectively.


IV. CONCLUSION
A wireless RF passive sensing technology has been proposed in this article which is capable of monitoring from very low temperature such -150 o C to very high temperature such as 600 o C with the help of a ceramic based sensor, SiO2 cable antenna, RVNA set up, and Turbotrack software which is developed by Sensatek. The accurate and reliable temperature measurements using this technology are demonstrably helpful for industries in continuous monitoring and predictive maintenance applications. We also established that this wireless high temperature monitoring technology performs quite well and accurately reflects the temperature of the monitoring unit even when installed inside a magnetized electric motor or generator without any measured electromagnetic or magnetically induced interference.
The real time wireless passive temperature sensing technology based on RF is a pathbreaking technology in the field of wireless sensing. This non-intrusive, robust technology can be installed easily and flexibly, even inside intricate geometries within electric motor or generator structures. This in turn helps industries for continuous monitoring of their components and performing predictive maintenance which can save them significant revenue each year. This cost-effective and reliable technology has immense potential, and it can improve many industries by upgrading performance, efficiency, and safety. Moreover, this wireless temperature sensing approach is quite unique in nature, and we believe that it can open new avenues for similar technologies such as pressure and strain sensing through progressive research and development.
Acknowledgment
This work is supported by the U.S. Air Force under AFWERX STTR Award Number: FA864920P1012
REFERENCES
[1] K. Bennion, “Electric Motor Thermal Research Annual Progress Report,” NREL Management Report NREL/MP-5400-67121, 2017, https://www.nrel.gov/docs/fy18osti/67121.pdf
[2] M. P. Boyce, Gas Turbine Engineering Handbook, 3rd ed. Amsterdam, The Netherlands: Gulf, 2006, ch. 19.
[3] Carlos R. Mejias-Morillo, Jayaprakash B. Shivakumar, Seng Loong Yu, Blake Roberts, Pedro Cortes, Eric MacDonald, Anton V. Polotai, Eduardo A. Rojas-Nastrucci, “High-Temperature Additively Manufactured C-Band Antennas Using Material Jetting of Zirconia and Micro-Dispending of Platinum Paste”, IEEE Open Journal of Antennas and Propagation, vol.3, pp.1289-1301, 2022.K. Abudu, U. Igie, O. Minervino, and R. Hamilton, “Gas turbine efficiency and ramp rate improvement through compressed air injection,” vol. 235, no. 4, pp. 866–884, Jun. 2020.
[4] N. Hasan, J. N. Rai, and B. B. Arora, “Optimization of CCGT power plant and performance analysis using MATLAB/Simulink with actual operational data,” Springerplus, vol. 3, no. 1, pp. 1–9, 2014, doi: 10.1186/2193-1801-3- 275.
[5] H.T. Cheng, S. Ebadi, and X. Gong, “A low-profile wireless passive temperature sensor using resonator/antenna integration up to 1000˚C,” IEEE AWPL, vol. 11, pp. 369-372, 2012.
[7] Hu K, Zhang G, Zhang W. Analysis and optimization of temperature field of high-speed permanent magnet motor. Advances in Mechanical Engineering. 2022;14(5). doi:10.1177/16878132221095914
[8] Deisenroth, D.C.; Ohadi, M. Thermal Management of High-Power Density Electric Motors for Electrification of Aviation and Beyond. Energies 2019, 12, 3594. https://doi.org/10.3390/en12193594
[9] Cisse, K.M.; Hlioui, S.; Belhadi, M.; Mermaz Rollet, G.; Gabsi, M.; Cheng, Y. Design Optimization of Multi-Layer Permanent Magnet Synchronous Machines for Electric Vehicle Applications. Energies 2021, 14, 7116. https://doi.org/10.3390/en14217116
[10] https://electrical-engineering-portal.com/basics-of-built-in-motorprotection-for-beginners
[11]https://www.motioncontroltips.com/what-are-thermal-overload-relays-andwhat-components-do-they-protect/