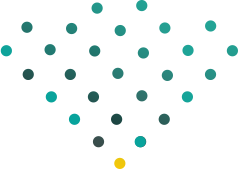
How on-blade sensors can increase power generation gas turbine efficiency in a control system
It is well established amongst gas turbine design engineers, as a rule of thumb, if the turbine inlet temperature (TIT) and by effect the 1st stage nozzle metal surface temperature is even 20°C above its operating limit, the life of the blade reduces by a factor of 3. For example, if the blade is design rated for 24,000 operating hours, operating at 20°C above this rated temperature reduces the blade life to 8,000 operating hours. This signifies the importance of measuring gas turbine blade surface temperatures with respect to accurately determining the remaining useful life of the blade.
The maximum allowable blade temperature plays a big role in determining maximum allowable TIT. Thus, the mean TIT for a given cycle depends on the maximum TIT and the TIT error. If the TIT error can be reduced, error in this case is the error due to using empirical relations instead of a direct temperature measurement, the mean TIT may be increased for a constant maximum TIT and the engine performance may be improved. The error due to the indirect determination of TIT from other parameters may be up to ±10°C. Increase in TIT by 7°C using directly measured TIT data instead of indirect determination using empirical relations in the fuel control system allowed for a 0.4% increase in thermal efficiency of the GT, power generation increased by 1.3% and the fuel consumption reduced by 0.3%. A direct measurement of the TIT or the 1st stage blade surface temperature also helps in creating accurate blade lifing models.
We also conducted a 1D control system simulation using integrated operational data from an existing GE 7EA Gas Turbine together with an additional 10 modeled data points depicting measured and calculated values from Sensatek wireless high temperature sensors mounted on the blade surface. This can be seen in Figure. The temperature sensors depicted are embedded in the first stage nozzle leading edge and is used to measure hot gas temperatures from the center of each transition piece outlet. Calculated values for Average/Mean, Spread 1, Spread 2, and Spread 3 were displayed on the same screen view. Sensatek and TTS created and merged conventional data, a set of data to represent the Sensatek wireless high temperature sensors by calculating a reasonable flame temperature (Tf) to be used as the average temperature for the Sensatek sensor array.
In the simulation, we calculated Tref by using the exhaust gas temperatures. A reasonable temperature spread between transition piece outlets was composed and fixed into the data used for the simulation. The spread had a rough correlation to exhaust spread, but the actual direct measurement of Tf is more accurate than conventional swirl calculations and we demonstrated this in the simulated data by conducting parametric variations of the swirl. The simulation of wireless sensors into prognostic system reveals direct measurements of actual firing temperature for each turbine nozzle, in a cannular, or annular chamber configuration. Actual firing temperature precisely point maintenance engineers to root causes of troublesome combustors. Enabling them to remedy temperature and emission spreads, and to run with smaller margins to design temperature limits. Benefits of this direct measurement include improving average turbine output by .5%, improving emissions by .7ppm nitrogen oxide and extending maintenance service intervals by 40%.