How Passive RF Sensors Work to Measure Blade Surface Temperature
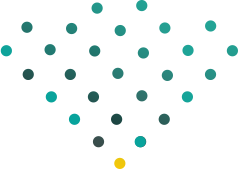
The surface temperature of a turbine blade is a strong indicator of engine health and blade life. Detecting these temperatures in a continuous, passive fashion is among the best ways of determining blade life and predicting maintenance needs.
Contact, Non-Contact, Active, & Passive Sensors
Heat sensing technology for gas turbines comes in two primary varieties: contact and non-contact sensors. Contact sensors are placed on an area of interest and detect surface temperatures directly. Non-contact sensors are typically optical, measuring infrared energy at a distance with a thermal imaging camera or spot pyrometer.
Within these categories, there are also active and passive sensor types. Active sensors generate and send out signals, pulses, or light to measure the reaction from the environment. Passive sensors simply receive information from the environment and let you know what they are picking up.
The issue with non-contact and active sensors is that optical measurements are inaccurate at higher temperatures and can suffer from significant emissivity errors. They also require more expensive technology that is costly to implement, maintain, and replace. A passive RF sensor, on the other hand, is both cost-effective and more accurate, with the ability to continuously amass valuable data on engine temperatures throughout the life cycle of the engine.
What Are Passive RF Sensors?
RF stands for Resonant Frequency. Contact-based surface temperature measurements are highly predictive of the life of gas turbine blades. A contact sensor patch can detect changes in the resonant frequency of the underlying surface, and calculate changing surface temperatures directly from this information. The sensors themselves can be quite small—perhaps the size of a postage stamp—lending them to large multi-sensor arrays with numerous data points throughout a turbine engine.
How Do RF Sensors Work?
As contact-based sensors, passive RF sensors absorb and precisely mirror the changes in the surface heat of the substrate. Ceramic-derived polymers are an ideal material for this purpose, as they can survive continuous extreme temperatures.
The sensors themselves come in the form of patches that bond to the turbine blade tips with strong adhesives. These low-profile, reflective patches will act as both resonators and antennas.
The dielectric constant of the substrate (e.g. a turbine blade tip) increases as the surface temperature rises, which simultaneously reduces the resonant frequency of the passive RF sensors. A transceiver sends out a pulsed wave with a wide frequency spectrum and tracks changes in the resonant frequency of all passive RF sensors in the array. Then, software charts and displays these measurements in real-time.
Advantages of Passive RF Sensors
Compared to pre-existing solutions, passive RF sensors such as those made by Sensatek are:
- Less expensive
- Easier to deploy (without a full engine teardown)
- Wireless
- More accurate
- Longer lasting
- Always at work in a passive manner
- Able to create rich, continuous life models of engine heat
Research and development on our sensors was funded by the National Science Foundation, Department of Energy, and NASA, with testing and verification by OEMs. With passive RF sensors powered by Seliken™, you’ll gain advanced control and real-time monitoring of blade tip health.
Sensatek sensors have been embedded and demonstrated with Siemens Energy on a SGT8000H Rotor, calibrated up to 1,300°C in laborator, and tested on a microturbine engine rotating wheel up to 127,000 rpm at 810°C. You can trust these sensors to perform in the harshest of environments, including Siemens gas turbine engines.
Get in touch with us to learn more about the potential benefits of RF technology and passive temperature sensors today.