How a Passive RF Sensor Can Enhance The Accuracy On An Infrared Camera
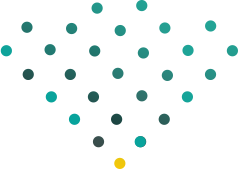
Resonant frequency (RF) and infrared (IR) sensors are fundamentally different technologies for detecting engine surface temperature. While each has its place, an RF sensor has a few distinct advantages—especially for continuous, real-time data in a passive sensor array. Not only is RF a more accurate technology in extreme environments, but a passive RF temperature sensor is more durable and easier to deploy alongside spot infrared thermometers, infrared scanning systems, and infrared thermal imaging sensors.
RF Sensor + Infrared Camera: Honing In on Engine Surface Temperature
The most basic difference is that our ceramic, passive RF sensor patches operate while in contact with the surface and collects engine surface temperature data from corresponding changes in resonant frequency, whereas an IR camera is a non-contact sensor that detects infrared radiation emitted from the surface at a distance. Here are a few more points to consider.
Infrared Camera Sensors: The actual temperature of a surface is merely inferred by measuring the amplitude of infrared energy emitted from the object. However, spot infrared thermometers and cameras must be configured to detect the most relevant portion of the IR band from the enormous 0.7 to 1000 micron range of IR wavelengths. The 0.7-14 micron band is most commonly employed for IR temperature measurements, but each application will require a unique camera model with the correct optic and detector types for the temperatures you expect to encounter.
Passive RF Temperature Sensors: The method of using RF to determine engine surface temperature is entirely different. As a contact-based sensor, any changes in surface heat of the engine will likewise affect the sensor directly. As the temperature increases, the resonant frequency drops. This is due to the increasing dielectric constant of the material (e.g. a gas turbine blade surface). A transceiver emits a pulsed, wide-frequency wave that surrounds the RF of the reflective patch sensor (the resonator) and tracks resonance changes in real-time for highly accurate measurements.
How Do RF Sensors Enhance the Accuracy of Infrared Cameras?
For starters, reliable test data has proven the unparalleled accuracy of a passive RF temperature sensor system. The average error of Sensatek RF sensor patches, for instance, is just 2.7 °C with a standard deviation of 0.73 °C. You can trust in the 95% confidence interval accuracy of ± 4.2 °C of this reliable and precise technology. For a 0-600°C range, for example, this would come out to an impressive ±0.71% accuracy, with a hysteresis of ±1.7 °C.
Here are a few other reasons that RF sensors help users have a major leg up:
- High Temperature Performance: Infrared solutions are known to suffer from accuracy issues in extreme temperatures. Optical measurements of any kind can also be expected to encounter emissivity errors on a regular basis. Our RF sensors are rated to perform in environments ranging from 25°C to 1,200°C (and even up to 1,750°C for short durations).
- Wider Frequency Spectrum: Unlike the more narrowly calibrated infrared technologies, our RF sensors repeatedly and rapidly ping the sensor with a wide frequency spectrum that allows for reliable, sensitive detection of both subtle and major shifts in the sensor temperature.
- Direct Measurement of Surface Temperature: There’s no better way to measure engine surface temperature than with a low-profile, contact-based sensor that syncs perfectly with the temperature of the surface to which it is attached.
- Wireless and Battery-Free: Every RF sensor operates entirely on small amounts of energy harvested from the signal put out by the RF transceiver. Since this is all the power the sensors need to function, there’s no other power source necessary and much less technology overall under stress within the engine. This makes it incredibly simple and cost effective to instrument numerous data points (such as different blade locations) for a more complete view of thermal engine performance.
- Longevity for Continuous Measurement: Our ceramic-derived passive RF sensors are simple low-profile patches that are smaller than postage stamps. They’ll avoid aerodynamic heating and endure incredibly high internal engine temperatures to provide long-term temperature life models throughout a full engine life deployment. With very little maintenance, it’s possible to amass much more nuanced data than less durable camera sensors that must be strategically deployed for planned tests.
This list showcases the true value of passive RF sensor precision. If you’re interested in learning more about our passive RF temperature sensors, contact Sensatek today or sign up for our pilot program!