4 Reasons RF Temperature Sensors Boost Gas Turbine Efficiency
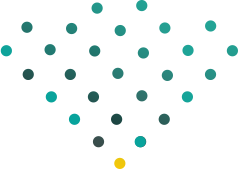
It takes great care and reliable data to optimize gas turbine efficiency. You’re trying to toe the line between maximum output and overloading the components in the engine, and every degree of engine heat has an impact. With RF temperature sensors, you can make confident adjustments to realize lasting efficiency gains.
How Do RF Temperature Sensors Boost Efficiency?
1. Precise Surface Temperature Trends
Accurate, nuanced, real-time, and continuous data on surface temperatures is your greatest ally in predictive maintenance and engine optimization. There is no other technology on the market that delivers the same level of precision in a convenient, cost-effective, easy-to-instrument fashion.
Wireless RF temperature sensors track subtle RF shifts that correlate with surface temperature. As a sensor’s temperature rises (via direct contact with the blade surface), its resonant frequency drops. The sensor acts as both a resonator and an antenna. A transceiver sends out wide frequency pulses to track changes in the RF of the sensors and software trends temperatures over time in a visual format.
This is a much more accurate and detailed method than the alternatives, such as standalone spot pyrometers or IR cameras. Optical technologies can be expensive and time-consuming to implement per data channel, and they also suffer from inaccuracies at higher temperatures due to the emissivity errors that affect all optical measurements.
Efficiency goals require precise data. RF temperature sensors deliver it.
2. Repeatable Measurements
Durable, ceramic patches are an ideal format for high-temperature sensors. They provide precise resonant frequency readings while surviving in extremely harsh environments for years of repeated measurements. They’re wireless and quick to deploy, even in hard-to-reach places, which makes it possible to instrument large numbers of blades for tens, hundreds, or thousands of data points.
Sensatek’s RF temperature sensors are rated for 40,000 hours at long-term temperatures up to 1,200°C. They’re designed to last the life of the engine and provide continuous data without any need for re-instrumentation. This gives you the ability to amass detailed life models of engine surface temperatures, identify issues by comparison with historical data, and carefully track efficiency gains over time.
3. Optimized Cooling Schemes
All of this data is exactly what you need to test and implement improved cooling schemes for maximum gas turbine efficiency. Optimized engine cooling is critical to efficiency because burning too cold minimizes output, but burning too hot damages components (leading to high costs from reduced blade life, shutdowns, maintenance, and reinstrumentation).
RF temperature sensors from Sensatek have been proven to provide outstanding measurement accuracy in tests, with an average error of just 2.7 °C and a standard deviation of 0.73 °C. Numerous and reliable temperature measurements will vastly accelerate your cooling optimization process.
4. Increased Lifespan on Turbine Engine Blades
Turbine heat has a profound effect on instrument survivability and component lifespans. Undetected hot spots in turbine engines can lead to substantial repair and maintenance costs or unplanned outages. The clear view of the engine surface temperature provided by an array of blade-mounted RF temperature sensors makes it simpler to manage engine performance, predict remaining blade life, and maximize component integrity.
The bottom line is that you’ll get more life out of your parts with access to precise temperature data. Improved blade lifespans will mean long-lasting instrumentation, reduced (and easily predicted) maintenance needs, and better engine performance.
Looking for more information on how RF temperature sensors can help you in the testing environment or in an active fleet? Contact us at Sensatek and share the details of your project. We’ll help you determine the potential value or impact of high-temperature sensors for your unique situation.