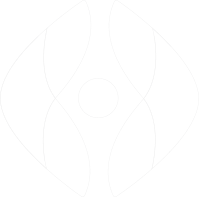
RF sensors built for gas turbines engines
Gain advanced temperature control with real-time health monitoring in the harshest of environments with passive rf sensors powered by Seliken™.
Sensatek’s passive rf sensor system provides continuous and real time measurement of temperature in-situ on stationary and rotating gas turbine blades.
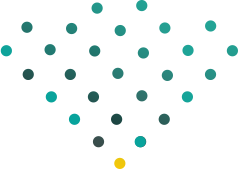
Explore the key benefits
Our real-time blade tip health monitoring system will:
- Extend the running time between maintenance outages
- Predict machine need for maintenance
- Increase energy production
- Extend the life of engines
- Reduce risk of failure
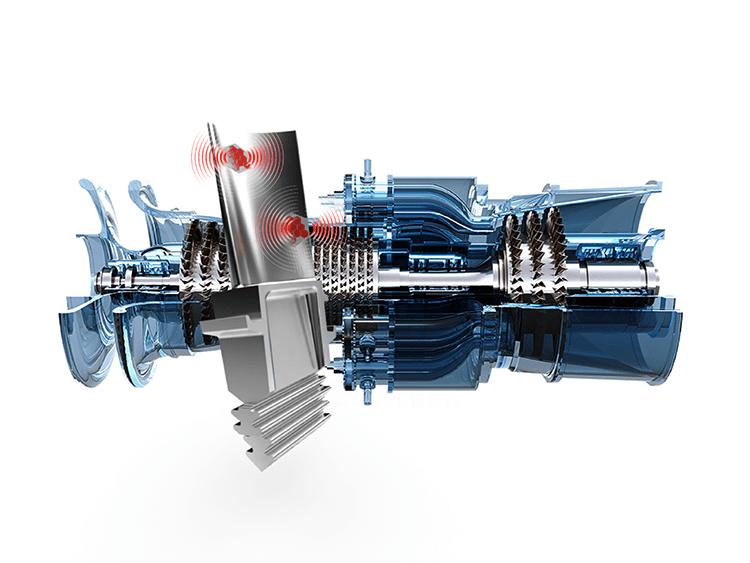
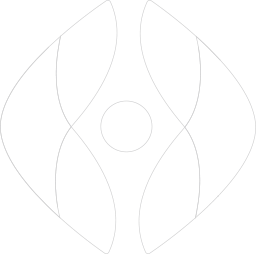
How it works
A low-profile reflective patch antenna behaves as both a resonator (sensor) and an integrated antenna. An interrogation circuit (transceiver) sends out a pulsed wave which contains a wide frequency spectrum surrounding the resonant frequency of the reflective patch sensor. When the temperature in the sensor increases, the resonant frequency reduces which is because the dielectric constant of the substrate material increases over temperature.
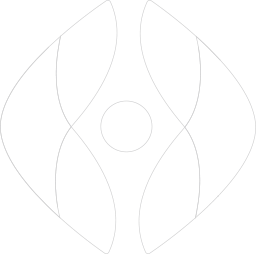
Proven practice with industry leaders
- Embedded and demonstrated with Siemens Energy on large gas turbines connected to the grid .
- Tested on small gas turbines for U.S. Air Force.
- Pilot demonstrations in progress with very large gas turbine engine manufacturers around the world.
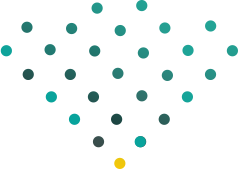
Technical Specifications
Sensor Size | Customizable from 10 millimeters to 21 millimeters in diameter, less than 1 millimeter in thickness |
Long Term Continuous Operating Temperature Range | 25°C to 1,200°C |
Maximum Temperature | Up to 1,750°C max for short durations |
Material Lifespan | Up to 40,000 hours at baseload operating conditions |
Materials | Polymer Derived Ceramics options that include Platinum, Nickel Alloy, and Alumina Ceramic |
Sensitivity | .4MHz / °C |
Accuracy | (+/- .3 - 2.5°C) |
Patents
- US 8,558,705 Ceramic Sensors for Wireless High Temperature Sensing
- US 8,860,532 Integrated Cavity Filter/Antenna System
- US 9,612,164 Low-profile Wireless Passive Resonators for Sensing
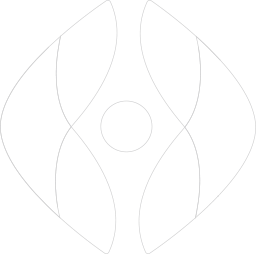
How Sensatek’s wireless sensor system compares
Since blade metal surface temperatures can dictate blade life and hence the maintenance cycle, it is extremely important to detect it directly rather than the gas flow temperatures. Our sensors provide temperature data in real time unlike other solutions that provides only the maximum temperatures experienced during engine tests.
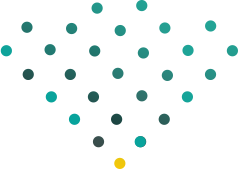
Ready to learn more about the future of propulsion technology?
Request your Proof of Concept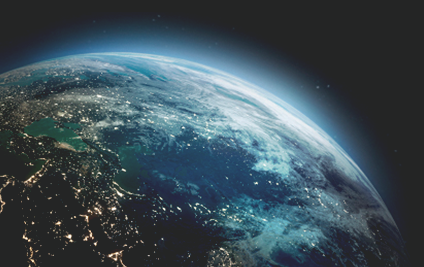