An Upgrade to Turbomachinery Surface Measurements in Turbine Engine Test Cells
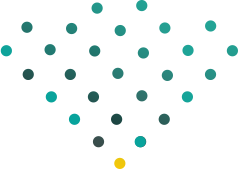
A turbine engine test cell is a carefully equipped location for performance checks and trial runs of a gas turbine engine (turbofan, turboprop, or turboshaft). The engine test cell is generally used for assessing the operating condition of the components and engine sections following maintenance and before deploying back in the field.
Jet engine test cells, for instance, ensure the safe and healthy operation of an engine before it is loaded back onto an aircraft. Adjustments can easily be made within an engine test cell, if necessary, to head off issues or inefficiency in the field. However, turbine engine test cells are also a crucial tool for test engineers during the engine development cycle.
The elements of a turbine engine test cell combine diagnostic and operational features (e.g. aerodynamic testing, fuel efficiency testing, stress testing) with protective features that safeguard the external environment. The design of induction and exhaust systems are critical for the stable operation of the engine, for instance, whereas a separate system is used to suppress the vibrations and noise in the outside environment and keep it within an acceptable limit.
Conventional Data Acquisition Systems
The design of the turbine engine test cell necessarily includes controls and equipment for data acquisition and analysis. Conventional data acquisition systems, however, must be installed in the area surrounding and outside of the engine — engines will come and go, while the test cell must remain independently functional.
The only exception will be instruments that you take the time to install within the engine during its testing period within the cell. These kinds of deep measurements can often require machining or drilling of holes for routing wires (perhaps for a thermocouple sensor harness), time-consuming engine teardowns, and costly re-instrumentation due to the limited survivability that internal measurements generally exhibit in the extreme environment of a gas turbine engine’s heat process.
Save Time & Money In Your Turbine Engine Test Cell
The best way to reduce the labor and high costs associated with robust internal testing instrumentation within the test cell is for the engine to come pre-equipped with the necessary sensors in a wireless array. Simply mount the engine within the turbine engine test cell, wirelessly connect to your network of internal sensors, and start amassing valuable data.
Sensatek has worked with the National Science Foundation, the Department of Energy, and NASA to develop and engineer a wireless RF sensor technology that makes this easy, fast, and far more cost-efficient than previous data acquisition technologies. The compact, wireless, ceramic-derived sensors provide you with:
- Capability to Instrument Numerous Data Channels: The tiny, wireless form factor (similar to a postage stamp) allows you to instrument a large number of sensors without dismantling the engine, even in hard-to-reach locations. Hundreds of data channels can be installed in the time it would normally take to deploy only several conventional optical measurements. Route every channel wirelessly to monitoring software that offers a complete picture of heat transfer performance.
- In-Situ Temperature Measurements: Contact measurements on the surface of turbine rotors, discs, and blades is more accurate and direct than non-contact, optical, or gas flow measurements. Our wireless RF sensors track subtle changes in temperature through direct contact with the part, ensuring the sensor matches the exact temperature of the surface.
- Real-Time Data: Realize data acquisition on a whole new level with continuous, real-time temperature data throughout a thermal cycle (and even throughout the life of the engine). While some other technologies are limited in their capabilities, perhaps indicating only the maximum temperature reached in engine tests, our wireless RF sensors provide a full historical model and alert you to uneven spikes in temperature in precise locations.
- Cost-Efficient Components: The polymer-derived ceramic body of our RF sensors enjoy high instrument survivability, reducing maintenance and replacement costs. They are also far less expensive per channel to deploy than optical sensors (pyrometers and IR cameras), with no costly wire harnesses, drilling, or engine modifications necessary.
Get in touch with our team of experts to learn how your engines can be outfitted with the perfect wireless sensor array to accelerate and optimize all diagnostic tests in the engine test cell — before the engine even gets there.