5 Musts in Spin Tests For Hot Section Components
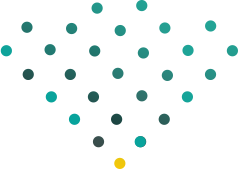
The hot gas path in a turbine engine is a treacherous place. Already among the most extreme of all man-made environments, turbine engines continue to grow hotter and spin faster as technology continues to define new limits on efficiency and performance. Look no further than the high-performance jet engines produced by Kratos Defense (which acquired Florida Turbine Technologies in 2019) for cruise missiles and unmanned aerial systems. Even their mobile test facilities must now accommodate engines with up to 3,000-lb. thrust.
These advances are made possible, in part, with robust data from test devices during the development cycle. Hot section components must endure complex and challenging thermal conditions, but so must the test devices that are monitoring their health.
5 Musts For Test Devices & Rotating Health Monitoring Systems
1. Long-Term Heat Resistance >650°C
The heat process will frequently operate at temperatures that exceed 650 °C, even in small gas turbines and at base operating loads. The TurboTrackTM sensor system from Sensatek has been subjected to heated spin testing by Aerodyn. Our instruments remained bonded to the wheel hub of an SW-140B microturbine throughout a 127,000 RPM test that reached a sweltering 810 °C (1,490 °F). These sensors can even withstand temperatures up to a maximum of 1,750 °C (3,182 °F) for short durations.
2. Adhesion At G-Loads >15,000g
Spin testing systems expose components to incredible centrifugal forces. This is a chemical challenge for adhesives that must keep sensors firmly affixed to all rotating components, not only because of the high g-loads but because they will occur in concert with extremely high temperatures. Carefully vet adhesives with heat spin testing to ensure reliable performance. Sensatek’s proprietary bonding mechanism has been demonstrated to withstand g-loads up to 16,000g of force at 10,500rpm (the rig maximum) without failure.
3. Survivability Throughout the Engine Life
The best rotating measurement systems are not only spin testing devices but have the long-term survivability to act as fleet health monitoring systems for the full life of the turbine without the need for re-instrumentation. TurboTrackTM rotating blade sensors have been strength-tested and verified by OEMs to withstand up to 40,000 hours of stress at baseload operating conditions in the field.
4. Compact Size For In-Situ Installation
A cumbersome rotating health monitoring system may necessitate the dismantling of the turbine in order to modify components and install the measurement locations. TurboTrackTM sensors are small and low-profile patch-style sensors that are often smaller than a postage stamp. This compact size enables “in-situ” installation, meaning it’s possible to deploy our wireless rotating monitoring system without removing a blade from the engine.
5. Wireless Communication
Routing a wiring harness throughout a turbine engine is a complex, expensive, and time-consuming process. Machining, drilling, partial or total engine teardowns, and other modifications may be necessary to accommodate the wiring. Spin testing devices are better served by a wireless system in which all sensors can communicate with the transceiver (and your monitoring software) as soon as they’ve adhered to the desired measurement locations.
Deploy a Proven Wireless Rotating Monitoring System: TurboTrackTM
Contact Sensatek today to learn more about TurboTrackTM technology from Sensatek. Our patented wireless rotating blade sensors make ideal test devices and also act as your perfect companion for continuous health monitoring in the field.
Brands like Florida Turbine Technologies and Kratos Defense already provide robust spin testing capabilities, but TurboTrack sensors offer an added capability to run high-speed heated spin tests and rig tests that truly test the limits. Generate continuous rotating measurement data on gas turbine engines and blades to put a stop to unexpected downtimes while saving time and money.